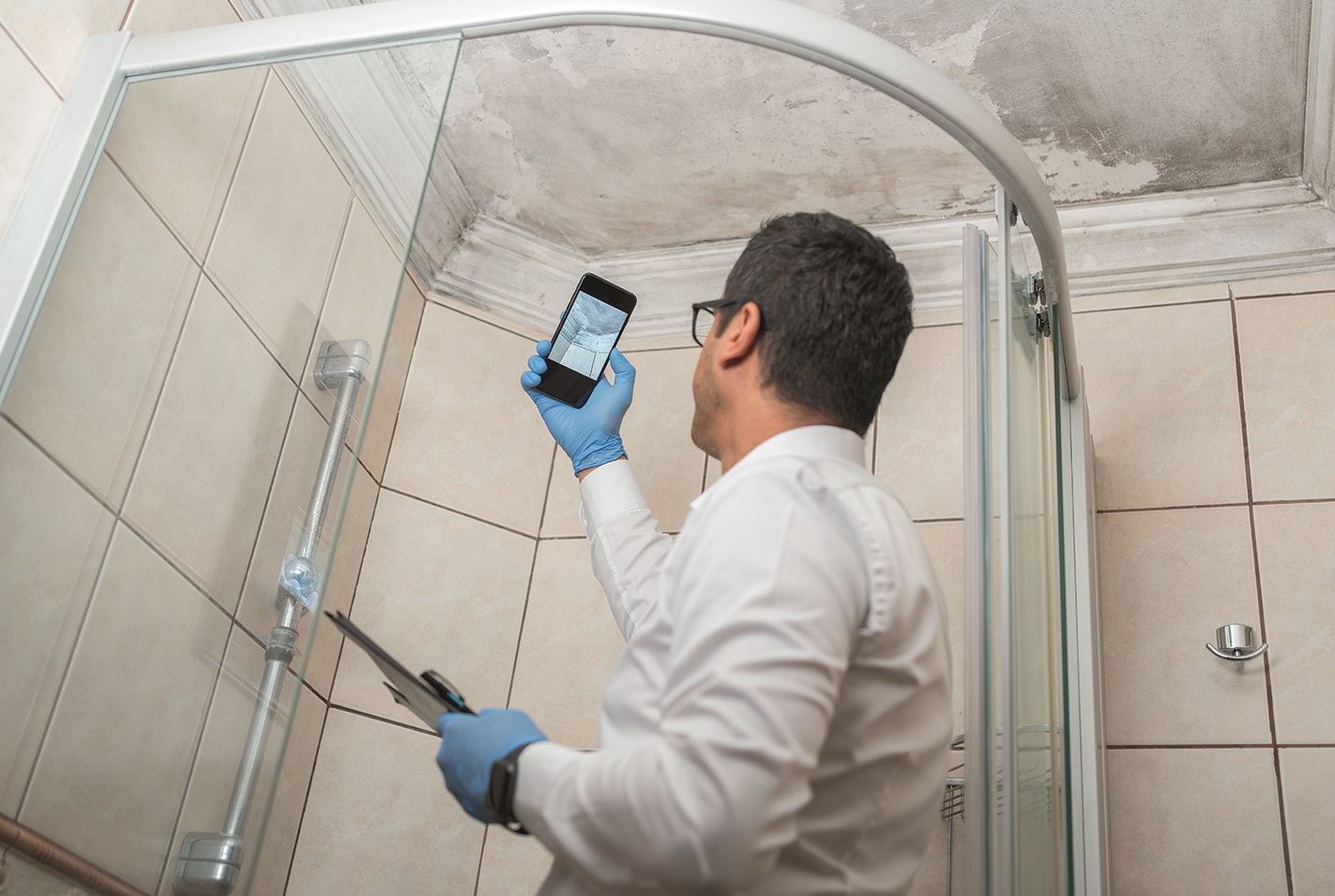
On the back of growing awareness of the health risks associated with mould exposure, building owners and facility managers should be taking a more proactive approach to mould remediation to ensure the well-being of employees and building occupants.
As a respected occupational health scientist who has worked around the world, Dr Brad Prezant has watched with interest at how a combination of flooding, high ambient humidity and poor indoor moisture management have in recent years caused significant mould problems in buildings.
Dr Prezant, managing director of consultancy Prezant Environmental, says as part of the debate about creating more resilient buildings, there must also be greater awareness of “vulnerable” construction materials that can contribute to a higher risk of moisture and mould damage in buildings. In addition, there may be a need to fine-tune the restoration process following events such as floods.
“The way you build the building can have a big impact on its vulnerability, the fungal growth,” says Dr Prezant, co-author of the book Recognition and Evaluation and Control of Indoor Mould.
For example, the widespread use of cheaper, composite wood products in construction, rather than the solid hardwood joists and bearers of the past, can leave a building exposed to mould and water damage.
“People can’t afford to build with solid Australian hardwood anymore, so they build with composite wood products. They’re good products and dimensionally stable,” Dr Prezant says.
“But if they get wet, it’s a big problem. We’re not going to change the way buildings are built. The evolution from solid wood to plywood to chip-wood products is a permanent thing because trees are a limited resource. But what we have to realise is that, when we use those materials that have that vulnerability, we need to design buildings with that in mind to help prevent those products from getting wet, as well as handle the maintenance appropriately.”
If flooding does occur with such products, Dr Prezant says it is crucial for restoration and clean-up teams to “get in there rapidly and manage the situation and dry them”.
Likewise, cleaners and restorers must be cautious about using some products that are billed as sustainable or natural.
“For instance, if people use certain essential oils as part of the remediation process and saturate the essential oils into the paper and gypsum of the wall lining, then a person who has a sensitivity to those substances comes into the space and they can’t remain in the space and occupy it.”
All in the planning
There is no doubt that global warming, higher rainfall levels, and increased flooding have put issues such as mould on the agenda in recent years.
In minor cases, mould can cause irritation of the eyes and skin, while for asthmatics the inhalation of mould spores can trigger an attack. Very rarely, people can develop a severe mould infection, usually in the lungs.
Lisa Michalson, director of Cleanstar XPOWER Australia, which distributes a range of cleaning machines, says the potential health impacts of mould are well understood.
She adds, however, that it can also have significant financial repercussions.
“Those financial impacts can include property damage, decreased property value, increased insurance costs and legal liabilities,” Michalson says.
For that reason, she says facility managers must be on top of issues such as water leaks, inadequate ventilation and poor maintenance practices whereby leaks and spills are not quickly addressed.
In terms of mould remediation, Michalson says it is crucial to follow industry remediation standards and to hire a professional mould-remediation company that uses high-quality equipment such as air movers, dehumidifiers and air scrubbers.
Such actions are all part of a day’s work for Danielle Hage-Downs, a restoration manager at AAT Restoration in Adelaide who says the business has seen a rise in demand in recent years for projects related to insurance losses, decontamination work and sanitisation.
She is clear when asked what is the most common error that facilities make when trying to target mould: “Failing to have a remediation plan!”
If an indoor environmental professional (IEP) has not yet been engaged, she recommends taking the following steps:
- Determine the degree of contamination – always thoroughly assess the project before starting any work.
- Assess the need for professional help – consider whether an IEP needs to be engaged for scoping, or perhaps only at an interim or post-remediation verification (PRV) stage.
- Set up and validate containments – ensure that cross-contamination does not occur as it could unnecessarily lead to another mould-remediation project having to be undertaken. This can include checking negative air pressure and ensuring there are no leaks between containment zones.
- Remove unsalvageable materials – this could include gyprock, insulation and other porous items with visible mould. Non-porous materials can be remediated using a dual approach of mechanical and chemical-based remediation.
While tomes have been written to discuss mould and what causes it, Hage-Downs says the factors for mould growth are simple – the presence of mould growth, nutrient sources such as organic substrate, any water source, the temperature and relative humidity, and oxygen. Add the impact of time and it is the perfect recipe for mould growth.
“Any water is the single most important factor for mould growth,” Hage-Downs says.
“That means mould growth can occur with any category of water. So, the best way to prevent mould is to keep materials dry or, if they get wet, to dry them quickly.”
She says AAT Restoration’s focus is on adhering to industry best practice, adding that the Institute of Inspection, Cleaning and Restoration Certification (IICRC) S520 for mould remediation promotes source removal, rather than the traditional reliance on chemicals, paints and coatings as a replacement.
“In my experience, chemicals, paints and coatings should be used as a complementary measure to source removal and encapsulants being used as a last resort following discussions and review with an indoor environmental professional,” Hage-Downs says.
Dr Prezant believes there needs to be a greater understanding within some sections of the restoration sector about which materials can be dried and salvaged after rain or flood events, and which materials are “too far gone” and need to be removed.
“But, definitely, a single response to just rip out all the plaster board or wall lining is not going to be appropriate for every job. That will be an overkill.”
Office market an impediment
For cleaners, restoration companies and building managers who are facing the curse of mould, Dr Prezant says the key is to determine what is causing the growth.
Are building materials mouldy because they got physically wet, or is the problem the result of the products absorbing moisture from their surroundings to such an extent that the threshold for fungal growth is surpassed (which is normally a water activity level of 0.65 or greater)?
“Then you can choose the appropriate solution,” he says.
“If the fungal growth is just superficial because of high ambient humidity, then maybe just a superficial cleaning and a change in the humidity status will address it because the fungal growth is not deep into the material, it’s just on the surface,” he says.
“On the other hand, if the plaster board is soaked up in liquid, that’s never going to suffice because now it’s being held by the gypsum plaster and no amount of superficial cleaning will work.”
Dr Prezant says while initiatives such as NABERS, the National Australian Built Environment Rating System, can contribute to better environmental performance, indoor air quality and mould mitigation in buildings, he acknowledges that such sustainability measures require a significant financial commitment from building owners and facility managers.
Furthermore, the impact of the pandemic – whereby more employees are working from home and companies have cut their office footprint – has had a massive impact on the financial viability of the office real estate market.
“It’s in the toilet, basically,” he says.
That, in turn, means budgets are tight. “Therefore, when office space is competitive and people are making money hand over fist, they’re excited to spend money on greening or sustainability types of things. But right now, they’re just struggling to keep their heads above water.”
The upshot is that factors such as mould mediation may be put on hold.
In considering the indoor environment, Dr Prezant hopes there will be a shift towards more sustainable measures such as ventilation of buildings, rather than relying on energy-hungry air-conditioners to cool rooms and reduce humidity.
While he believes there are few examples of poor moisture management from internally generated moisture in commercial environments, it is a different story in many residential settings, where fans may not be functioning properly in bathrooms and kitchens, and appliances such as rice-cookers could add to moisture build-up.
“And what we saw happening in NSW and Queensland this past year when the ambient humidity was really high was that all of that additional humidity in people’s homes often pushed it over the edge to the point where they were getting condensation on the inside of the building and fungal growth.”
Dr Prezant thinks more can be done through government, national building codes and Standards organisations to ensure that building design addresses issues such as ventilation and mould mitigation.
He sits on the ASHRAE Standard SPC241 committee that in coming months will develop a national standard for infection control and ventilation. Such standards could be useful in so much as they are adopted into building codes.
“For example, when it comes to mould, there could be a standard that says you can’t vent your clothes dryer into the occupied space of a building – you have to exhaust it to the exterior. We are also looking now at doing that for bathrooms and for kitchens so that it has to exhaust to the exterior as opposed to the roof cavity.”
Do your homework on remediation providers
As cleaning contractors and restorers tackle mould remediation in an era of increasing natural disasters and flooding, they should be getting the appropriate training and education to adopt industry best-practice processes.
Michalson also believes that relatively new technologies such as specialised fogging machines – which distributes a fungicidal solution that penetrates surfaces and eliminates mould growth – can make a difference.
Likewise, UVC light radiation technology that kills mould spores and stops them from spreading is increasingly on the radar.
The other factor is for facility managers to hire suitably qualified remediation service providers. Michalson says it is crucial to do your homework before engaging a restoration or remediation contractor.
She advises researching potential companies, ensuring that a company has the requisite licensing and insurance to perform mould remediation services; getting multiple quotes; asking the company to provide a detailed explanation of their remediation process and the expected outcomes; and insisting on providers that have the relevant certifications.
“And make sure that all details of the remediation process are outlined in a written contract, including the scope of work, timeline and pricing,” Michalson says.
Hage-Downs agrees that it is important to check the credentials of providers and to engage a suitably qualified company that has contemporary knowledge of industry best practice.
“Remember that mould is potentially hazardous and many facility managers are unaware of the significant dangers or the correct processes involved in removing mould from facilities safely and adequately,” she says.
“Therefore, it is important to do your research and identify the right provider for you. Reputation is everything and you should not shy away from asking for project examples and references.”
This first appeared in the May/June issue of INCLEAN magazine.
Comment below to have your say on this story.
If you have a news story or tip-off, get in touch at info@incleanmag.com.au
Sign up to INCLEAN’s newsletter.